RageKage
Member
Well thanks to WJCO I've decided to tackle regearing myself. Figured I'd do the front first since it's a take off Rubicon axle and it's not on the Jeep yet. Everything is going smooth so far. Just painted the gears to check the pinion depth and want to see other opinions on the markings. I'm finding it hard to actually see very defined marks.
View attachment 306043View attachment 306044View attachment 306045
Did a quick search for correct patterns hopefully this helps. I think yours is too deep.
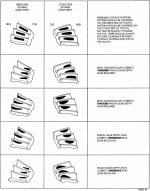
Sent from my iPhone using WAYALIFE mobile app