Rock40
Active Member
Blasted the clutch pedal to clean it up, new needle bearings are on the way
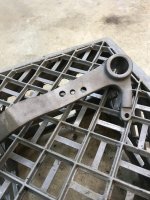
Brake pedal, to my surprise, the factory pivot pins fits the hydroboost rod perfectly. However it wasn't in the right spot. The pin is pressed into place. I ground the one end off and then pressed the pin out hydraulically. Notice that the pedals really only ever got "half" painted, essentially from overspray when the truck was built
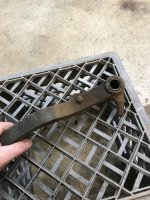
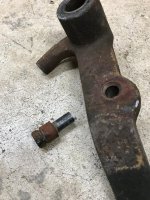
Cleaned it up to get it ready for welding. The pedal is cast steel and I made a bracket out of 3/8" plate in order to move the pivot point further out from the firewall (towards the driver).
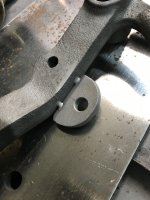
I was a bit nervous to weld on the braking system, especially the main pivot point. However if this ever breaks loose I'll be astounded (and probably dead). Double pass TIG, it welded very nice
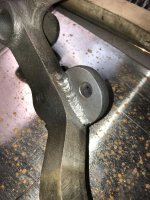
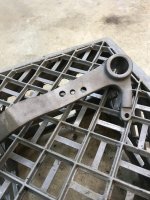
Brake pedal, to my surprise, the factory pivot pins fits the hydroboost rod perfectly. However it wasn't in the right spot. The pin is pressed into place. I ground the one end off and then pressed the pin out hydraulically. Notice that the pedals really only ever got "half" painted, essentially from overspray when the truck was built
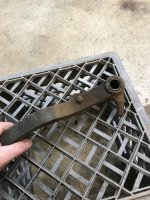
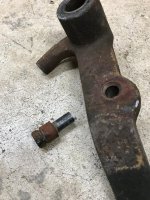
Cleaned it up to get it ready for welding. The pedal is cast steel and I made a bracket out of 3/8" plate in order to move the pivot point further out from the firewall (towards the driver).
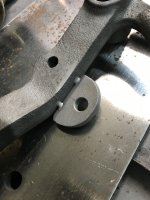
I was a bit nervous to weld on the braking system, especially the main pivot point. However if this ever breaks loose I'll be astounded (and probably dead). Double pass TIG, it welded very nice
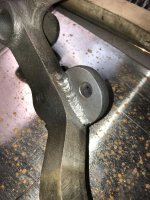